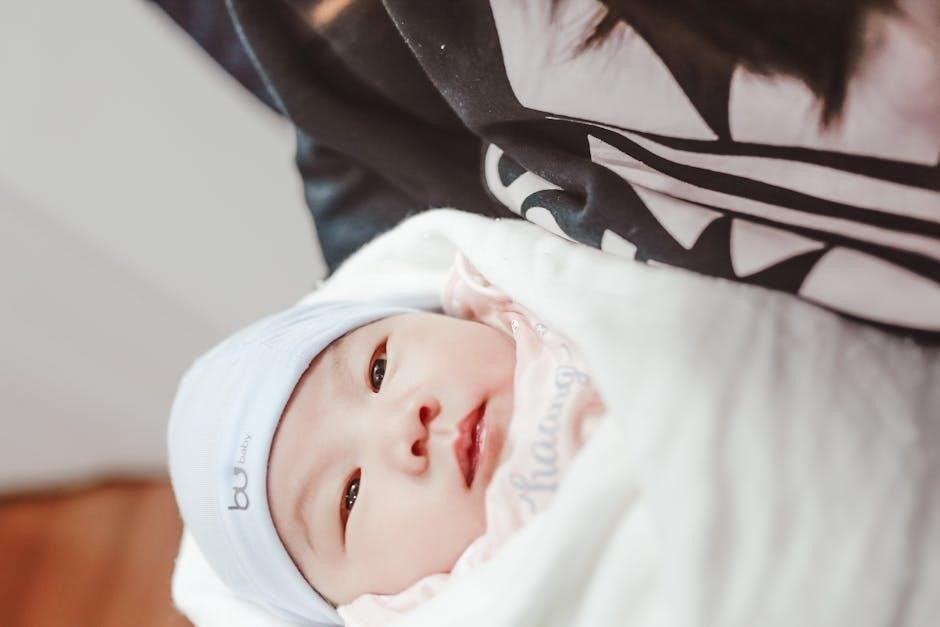
An SDS cover sheet is a crucial document for organizing safety data sheets in binders, ensuring compliance with OSHA and GHS standards while promoting workplace safety and efficiency.
1.1 Definition and Purpose of SDS Cover Sheets
An SDS cover sheet is a document designed to organize Safety Data Sheets (SDS) in a binder, ensuring compliance with OSHA and GHS standards. Its purpose is to provide a centralized location for chemical information, enhancing workplace safety and efficiency. It typically includes labels for the binder spine and front, making it easy to identify and access SDS documents quickly during emergencies or audits.
1.2 Importance of Organizing Safety Data Sheets
Organizing Safety Data Sheets (SDS) is essential for workplace safety and regulatory compliance. A well-structured SDS binder ensures quick access to critical chemical information during emergencies, reducing risks and improving response times. Proper organization also simplifies compliance with OSHA and GHS standards, making audits more efficient and ensuring all safety protocols are met effectively.
Structure and Components of an SDS Cover Sheet
An SDS cover sheet typically includes a binder spine label, front cover details, emergency contacts, and a list of contained SDS documents, ensuring easy identification and access.
2.1 Standard Elements of an SDS Binder Cover
A standard SDS binder cover includes a clear title, binder ID, department name, emergency contact details, and building/room numbers. It also lists the range of SDS documents inside, ensuring easy identification and access. Compliance with OSHA and GHS standards is highlighted, along with a spine label for quick recognition on shelves. These elements ensure organization and quick access in emergencies.
2.2 Labels for Binder Spine and Front Cover
Labels for the binder spine and front cover are essential for quick identification. The spine label typically includes the binder ID, department name, and SDS range, while the front cover features the title, building/room numbers, and emergency contacts. These labels ensure clarity and easy access, making it simpler to locate specific SDS documents in high-pressure situations. Proper labeling enhances organization and compliance with safety standards.
Creating an SDS Binder Cover Sheet
Creating an SDS binder cover sheet involves downloading a PDF template, customizing it with specific details, and ensuring it meets OSHA and GHS standards for workplace safety.
3.1 Downloading Templates in PDF Format
Download SDS cover sheet templates in PDF format from websites like kendriedger.com or pdfFiller. These templates are free, editable, and printable, designed for 3-ring binders. They include pre-designed labels for the spine and front cover, ensuring a professional look. Many templates are customizable to fit specific workplace needs, saving time and ensuring compliance with safety standards. Popular options include Chemical Safety’s SDS database and the University of Cincinnati’s binder covers.
3.2 Customizing the Cover Sheet for Specific Needs
Customize SDS cover sheets to meet workplace requirements by adding company logos, department names, or specific chemical information. Editable PDF templates allow users to insert emergency contact details, building numbers, and other relevant information. Color coding and organizational labels can enhance clarity. Ensure all customizations align with OSHA and GHS standards for compliance and effectiveness in managing safety data sheets efficiently.
Legal and Regulatory Compliance
Compliance with OSHA standards and GHS guidelines is essential for SDS organization. Properly formatted cover sheets ensure adherence to legal requirements and promote workplace safety effectively.
4.1 OSHA Standards for SDS Organization
OSHA requires employers to maintain Safety Data Sheets (SDS) in an organized and easily accessible format. Under standard 29 CFR 1910.1200, SDS must be readily available to employees, ensuring quick access during emergencies. Proper labeling and clear identification of SDS binders are essential. Employers must also ensure SDS are updated regularly and include emergency contact information, adhering to both OSHA and GHS guidelines for workplace safety compliance.
4.2 Ensuring Compliance with GHS Guidelines
Compliance with GHS guidelines is essential for proper SDS organization. GHS standards require clear labeling, including hazard pictograms and precautionary statements, to ensure safe chemical handling. Using standardized SDS cover sheets helps meet these requirements by providing a consistent format for organizing and displaying critical safety information. Regular audits and updates are necessary to maintain compliance and ensure all SDS are accurate and accessible in the workplace.
Best Practices for Maintaining an SDS Binder
Regularly update SDS documents, ensure accessibility, and maintain a centralized location for easy access. Use clear labels and organize sheets alphabetically for efficient retrieval and compliance.
5.1 Regular Updates and Revisions
Regularly updating SDS documents ensures compliance with changing regulations. Employers must review and replace outdated sheets, incorporating new safety information to maintain workplace safety. This practice prevents risks associated with incorrect data, ensuring all staff have access to current safety protocols. Updates should be logged and communicated to relevant personnel to avoid misinformation and enhance preparedness for emergencies.
5.2 Accessibility and Visibility in the Workplace
Ensuring SDS binders are easily accessible and visible is critical for workplace safety; Binders should be placed in central locations with clear labels, allowing employees to quickly locate vital information during emergencies. Regular audits should confirm that all materials are up-to-date and properly organized. Visibility and accessibility not only enhance safety but also support compliance with regulatory standards, ensuring a safer work environment for all personnel.
Digital vs. Physical SDS Binders
Digital SDS binders offer easy updates and accessibility, while physical binders provide quick, tangible access. Both options ensure compliance and workplace safety, catering to different preferences and needs.
6.1 Advantages of Digital SDS Management
Digital SDS management enhances accessibility, enabling quick searches and updates. It reduces storage space, minimizes physical handling, and allows real-time access across devices. Automated updates ensure compliance, while cloud storage provides backup and recovery options. Digital systems also support environmental sustainability by reducing paper use, making them a modern, efficient alternative to traditional physical binders.
6.2 Benefits of Physical Binders for Quick Access
Physical binders provide immediate tactile access to SDS, eliminating reliance on digital devices. They ensure consistent organization, with clear spine and cover labels for easy identification. Durable and long-lasting, physical binders are less prone to technological issues, making them a reliable backup. Their visibility and accessibility make them ideal for quick reference, especially in emergencies or areas with limited digital resources.
Emergency Information and Contacts
SDS cover sheets should include emergency contact details, such as phone numbers and department names, to ensure quick access during chemical incidents or spills.
7.1 Including Emergency Contact Details
Including emergency contact details on an SDS cover sheet ensures quick access during incidents. It typically features phone numbers, department names, and building/room numbers for rapid response. This information aids in connecting with the right personnel swiftly, adhering to safety protocols and regulatory standards. Clear labeling of emergency contacts enhances workplace safety and preparedness for chemical-related emergencies or spills.
7.2 Procedures for Handling Chemical Emergencies
Procedures for handling chemical emergencies should be clearly outlined on the SDS cover sheet. This includes evacuation routes, spill containment measures, and first aid instructions. It may also reference specific SDS sections for detailed protocols. Ensuring these procedures are easily accessible enhances preparedness and compliance with safety regulations, minimizing risks during incidents.
Industry-Specific SDS Requirements
SDS cover sheets must be customized for various industries such as healthcare, manufacturing, and construction to meet specific regulatory and operational requirements effectively.
8.1 Customizing for Different Work Environments
SDS cover sheets can be tailored to fit specific workplace needs, such as healthcare, manufacturing, or construction. Customization ensures that critical safety information, emergency contacts, and handling procedures are readily accessible and relevant to the work environment. This adaptability enhances compliance and safety, making it easier for employees to access vital data quickly in emergencies.
8.2 Examples of Industry-Specific SDS Covers
Examples of industry-specific SDS covers include healthcare, with biohazard symbols and medical emergency contacts, and manufacturing, focusing on chemical handling and spill procedures. Construction covers might emphasize site-specific safety protocols and emergency evacuation plans. These tailored designs ensure critical information is immediately accessible, enhancing workplace safety and compliance with industry standards.
Designing an Effective SDS Cover Sheet
Design an SDS cover sheet with clarity and compliance in mind. Use bold headings, color coding, and bullet points to highlight key information like emergency contacts and chemical lists.
9.1 Tips for Clear and Concise Labeling
Ensure labels are legible and straightforward. Use large fonts for headings, bold critical information, and avoid clutter. Include essential details like binder contents, emergency contacts, and building numbers. Apply color coding for quick identification and maintain consistency across all SDS binders for easy access and compliance with safety standards.
9.2 Using Color Coding for Better Organization
Color coding enhances readability and organization. Use distinct colors for different chemical categories, hazard levels, or departments. Apply color-coded labels or tabs to binder spines and covers for quick identification. Consistent color schemes ensure clarity and efficiency, making it easier to locate specific SDS sheets. This method aligns with safety standards and improves accessibility in emergency situations.
Free Resources and Templates
Access free SDS cover sheet templates in PDF format from websites like kendriedger.com. These editable and printable resources help organize safety data sheets efficiently.
10.1 Popular Websites for Downloading SDS Templates
Popular websites like kendriedger.com, ChemWatch, and ILPI offer free SDS cover sheet templates in PDF format. These sites provide editable and printable options, ensuring compliance with OSHA and GHS standards. They are reliable sources for customizable templates, making it easy to organize safety data sheets efficiently. Visit these platforms to download high-quality templates tailored to your needs.
10.2 Printable and Editable PDF Options
Printable and editable SDS cover sheet PDFs are widely available, offering flexibility for customization. Websites like pdfFiller provide cloud-based solutions for easy editing and printing. These templates allow users to input specific details such as building numbers, emergency contacts, and department names, ensuring a tailored approach to safety data organization and compliance with regulatory standards effectively.
Common Mistakes to Avoid
Common mistakes include using incomplete or outdated information and poor organization of SDS documents, which can lead to non-compliance and safety risks. Always ensure accuracy and proper categorization.
11.1 Incomplete or Outdated Information
Using incomplete or outdated information on SDS cover sheets can lead to non-compliance with OSHA and GHS standards, creating safety risks. Ensure all details, such as emergency contacts, building numbers, and chemical specifics, are accurate and up-to-date. Regularly update SDS documents and cross-reference them with the latest versions to maintain compliance and workplace safety.
11.2 Poor Organization of SDS Documents
Poor organization of SDS documents can lead to delays in accessing critical safety information during emergencies. Disorganized binders or digital files may result in compliance issues and increased safety risks. Ensure SDS documents are clearly labeled, categorized, and regularly updated to maintain easy access and readability, adhering to OSHA and GHS standards for workplace safety.
Training and Awareness
Proper training ensures employees understand SDS usage, organization, and updates, promoting a safer workplace and compliance with safety standards through regular, informative sessions and resources.
12.1 Educating Employees on SDS Usage
Training employees on SDS usage is vital for workplace safety. It involves familiarizing them with accessing, interpreting, and updating SDS documents. Regular sessions should cover understanding chemical hazards, handling procedures, and emergency protocols. Employees should learn to navigate SDS binders, both physical and digital, ensuring they can quickly locate and use critical safety information. This education promotes compliance and a safer work environment.
12.2 Regular Updates and Training Sessions
Regular updates and training sessions are essential for maintaining SDS compliance and employee safety. Employers should schedule periodic training to review SDS formats, updated hazard information, and emergency procedures. This ensures employees stay informed about new regulations and can effectively use SDS resources. Regular reviews of SDS binders, both physical and digital, help keep documents current and accessible, promoting a safer workplace environment through continuous education and adaptation;
Case Studies and Examples
Real-world examples demonstrate effective SDS binder implementations, such as Henry Schein NZ adapting SDS for compliance, ensuring workplace safety and streamlined chemical management across industries like manufacturing and healthcare.
13.1 Successful Implementation of SDS Binders
Companies like Henry Schein NZ and the University of Cincinnati successfully implemented SDS binders, ensuring compliance with safety standards. Their use of PDF templates and customizable covers improved organization and accessibility. These examples highlight clear labeling, emergency contact details, and adherence to OSHA and GHS guidelines, demonstrating how effective SDS management enhances workplace safety and efficiency.
13.2 Lessons Learned from Real-World Scenarios
Real-world implementations reveal common challenges like outdated information and poor organization. Companies such as Henry Schein NZ and the University of Cincinnati highlight the importance of regular audits and employee training. Ensuring SDS binders are easily accessible and clearly labeled has proven critical for compliance and emergency preparedness, avoiding potential safety risks in the workplace.
Future Trends in SDS Management
Digitalization and automation are revolutionizing SDS management, enabling real-time updates and seamless integration with safety systems, enhancing compliance and efficiency in maintaining safety data sheets.
14.1 Digitalization and Automation
Digital tools and automation are transforming SDS management by enabling real-time updates, cloud-based access, and integration with safety systems. These advancements ensure compliance, reduce errors, and improve accessibility, making it easier for organizations to maintain accurate and up-to-date safety data sheets while streamlining their safety protocols and emergency response procedures efficiently.
14.2 Integration with Safety Management Systems
Integrating SDS binders with broader safety management systems enhances overall workplace safety by linking chemical data with hazard assessments, training records, and incident reports. This holistic approach ensures seamless access to critical information, fostering compliance with regulations like OSHA and GHS while improving risk management and employee training programs, ultimately creating a safer and more organized work environment for all employees.
An SDS cover sheet is vital for organizing safety data, ensuring compliance with OSHA and GHS standards, and promoting workplace safety and efficiency.
15.1 Summary of Key Points
An SDS cover sheet is essential for organizing safety data, ensuring compliance with OSHA and GHS standards. It provides a clear structure for binder organization, customization options, and accessibility. Including emergency contacts and essential details ensures workplace safety. Regular updates and visibility are crucial for maintaining compliance and efficiency in handling chemical information.
15.2 Final Thoughts on Effective SDS Management
A well-organized SDS binder with a clear cover sheet is vital for workplace safety and regulatory compliance. Regular updates, accessibility, and inclusion of emergency contacts ensure preparedness. Proper labeling and customization enhance efficiency. By maintaining a structured SDS system, organizations prioritize employee safety and adherence to standards, fostering a safer and more compliant work environment.